協働ロボットと人間の連携が生む新しい働き方
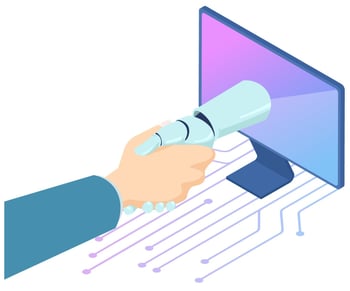
これまで産業用ロボットを活用した自動化に関するノウハウや事例をご紹介してきました。その他、AGVやAMRなどの無人搬送車に関するご紹介、IoT機器の活用方法など、工場のFA化に関わる分野を中心に見てきました。今回は、これまでご紹介していなかった協働ロボットについて一緒に見ていきましょう。
1.協働ロボットと産業ロボットの違いとは?
協働ロボットは、人との協働作業を前提に設計されたロボットです。最大の特徴は、安全機能が組み込まれており、専用の安全柵なしで人と同じ空間で作業できる点です。一般的な協働ロボットはセンサーによって人との接触を検知すると即座に停止します。また、力の制限機能があり、万が一接触しても重大な事故につながりにくい設計です。一方、産業ロボットは高速・高精度な作業ができ、様々な作業に適応可能ですが、大きな力や速い動きを必要とする作業で活躍することが多いです。安全柵の設置が必須となりますが、生産性と効率性において優れた性能を発揮します。特に、大量生産ラインでの定型作業や、人では困難な高負荷作業を自動化する際に採用されることが多いです。
両者の技術的な違い、主な違いは以下の通りです。
可搬重量:産業ロボットは数百kg以上の重量物も扱えますが、協働ロボットは最大で35~50kg程度まで
動作速度:産業ロボットの方が大幅に速い
プログラミング:協働ロボットは直感的な操作が可能、産業ロボットは専門知識が必要
設置スペース:協働ロボットの方がコンパクトで、設置が容易
2.導入における具体的なハードルと課題
【導入時のコストと費用対効果】
協働ロボット:
・初期投資は比較的少額(300万円~)※1
・安全柵が不要でコスト削減
・柔軟な配置転換が可能
産業ロボット:
・初期投資が高額(数百万円~)※1
・安全柵や周辺設備のコストが必要
・設置工事費用や工数も考慮が必要
※1・・・金額に関しては確認が必要です。目安としてお考えいただければ幸いです。
【安全性とコンプライアンス対応】
協働ロボットであっても、リスクアセスメントは必須です。特に以下の点に注意が必要です。
・作業内容に応じた安全認証の確認
・作業者への安全教育の実施
・定期的な安全点検の実施
・関連法規制への対応
【現場での適応性と設置の難易度】
導入時には以下の課題に直面することが多くあります。
1.既存の生産ラインとの統合
2.作業者の受け入れ態勢
3.作業スペースの確保
4.電源や配線の整備
3.課題解決のためのアプローチと解決策
【導入前の準備と現場の調査】
成功のためには、以下のステップが重要です。
1.現状の作業分析と課題の明確化
2.導入目的の設定と期待効果の算出
3.作業者との合意形成
4.段階的な導入計画の策定
【トレーニングと技術支援の活用】
・メーカーが提供する研修プログラムの活用
・社内技術者の育成計画の策定
・外部専門家との連携体制の構築
4.協働ロボットと産業ロボットの選び方チェックリスト
【自社の作業内容に応じた選択基準】
□ 作業の種類と内容
□ 必要な可搬重量
□ 要求される精度
□ 作業速度の要件
□ 設置スペースの制約
【投資対効果の検討ポイント】
□ 初期投資額
□ ランニングコスト
□ 期待される生産性向上
□ 人件費削減効果
□ 保守費用の見積もり
5.サカエからの協働ロボット導入事例をご紹介
【ディスクSET確認機】
FANUCの協働ロボットCRXを導入したディスクSET確認機です。導入前は手作業での確認作業が行われており、常に作業者が必要でした。導入後は、ロボットがディスクの積層と検査を行うことで、0.5人分の工数を削減し、作業者は他の工程に集中できるようになりました。この結果、全体の作業効率が向上し、さらなる省人化を検討するきっかけとなりました。
詳しくはこちらの記事をご覧ください。
6.まとめ
協働ロボットと産業ロボットは、それぞれに特徴があり、用途に応じて使い分けることが重要です。導入に際しては、以下の点を特に意識しましょう。
1. 作業内容と必要な機能の明確化
2. 安全性とコンプライアンスへの配慮
3. 導入後のサポート体制の確認
4. 段階的な導入によるリスク軽減
今後、両者の技術はさらに進化し、より使いやすく、より安全なものとなっていくことが期待されます。自社の状況に合わせて最適な選択を行い、効果的な導入を実現しましょう。導入に際する不安、進め方に懸念点がありましたら、お気軽に弊社までご相談いただければ幸いです。